Introduction
- The concept of Common Effluent Treatment plant is to treat the same type of Effluent generated from clusters of Industries.
- It’s effective method to achieve the standard parameters (PH,TSS,TDS, O&G) to improve the quality of water.
- The main purpose of CETP is to reduce the treatment cost of effluent released by group of industries &easy monitoring.
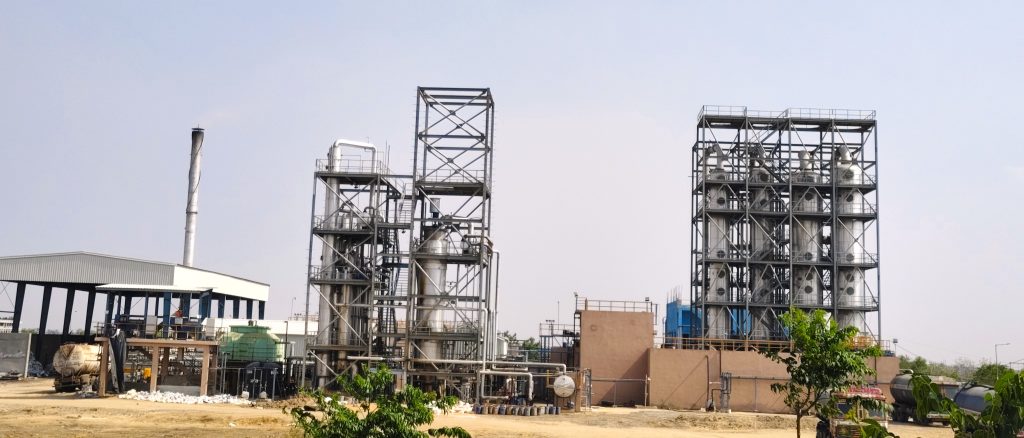
Types of CETP effluents

Types of CETP effluents
Effluent generated from:
- Complex Organic Industries : Pesticides, Pharmaceuticals, Paints, Dyes, Petrochemicals, Detergents, Pesticides.
- Electric power plant : Lead, Mercury, Cadmium, Chromium, Arsenic
- Iron and steel industry : Ammonia, Cyanide, phenols, Naphthalene.
- Paper and Pulp Industries: Dioxin, furans.
Treatment of Industrial waste water
OIL & GREASE REMOVAL
- The effective removal of Oil &Grease is dependent on the characteristic of the oil (Suspension state and droplet size)
- CETP contains free oil, Heavy oil, Emulsified oil, and dissolved oil.
- Plate pack oil and water separator, chemical treatment via DAF, Chemical treatment via Centrifuges and media filters are the different technologies related to remove the oil and grease in CETP.
EQUALIZATION PROCESS OF CETP
- Act as buffer , that make effluent homogenous by mixing.
- Flash mixer will balance the PH value of the effluent by chemical dossing process.
- Aeration process in Equalization tank will reduce the VOC content of the effluent by oxidation process.
SOLIDS REMOVAL PROCESS
- Solids can removed using sedimentation with solids recovered as slurry or sludge.
- For sedimentation process coagulant, flocculants are required.
- For increasing the fast sludge settlement poly electrolytes can use.
- Tube settler, Plate settler, HRSCC can used for the fast solids settlement process. it will minimize the treatment time and area of tank construction.
REMOVAL OF BIODEGRADABLE ORGANICS
- It is the treatment process by using oxygen and microorganisms to biologically oxidize the organic pollutants and producing waste sludge (floc) containing oxidized material.
- ASP,MBBR,MBR,SBR are the different type of biological oxidation process.
- Pure oxygen from oxygen generator will multiply the microbes and degrade the bio organics.
REMOVAL OF INORGANICS
- Synthetic organic materials includes solvents, paints pharmaceuticals, pesticides can be difficult to treat.
- The treatment methods are often specific to the material being treated.
Methods of treatment:
- Advance oxidation process (Electrocoagulation/ionization/ozonation)
- Evaporation and Solvent stripping
- Chemical precipitation/Immobilization.
ZERO LIQUID DISCHARGE SYSTEM
Main aim of ZLD is to recover useful products and salts from reject, apart from recovery of maximum water for recycle. ZLD Technologies :
- Solvent Extraction/Stripping
- Ultra filtration /Reverse Osmosis
- Evaporation technologies
- Agitated Thin film Dryer
- Incinerator/calcinatory/crystaliser.
BRINE TREATMENT
- Brine treatment involves removing dissolved salt ions from the waste stream.
- Brine treatment system involves maximum recovery of fresh water or salt.
Brine treatment methods:
- Membrane filtration process: RO Plant
- Evaporation process: MEE,ATFD,MVRE
- Ion exchange process.
SLUDGE DEWATERING MECHANISM
- Decanter centrifuge : separate solids from liquid or slurry by using high centrifugal force to the induce sedimentation. Decanter centrifuge produce solid cake material that is suitable for mechanical handling.
- Belt Press: rollers and belt to dewater material by passing the slurry to different zone by using chemicals. dewatered material that varies in consistency depending on the solids concentration of the feed.
- Filter Press: filter press provide highest level of mechanical dewatering without the use of chemicals. dewatered sludge is in the form of cake.
Treatment of Industrial waste water

Our Vision
Our Mission
Our Values
To continuously strive to achieve highest standards of quality services in concurrence with client’s expectations on a professionally cost-effective manner.
To build long term relationship with our clients and provide exceptional customer services by pursuing business through innovation and advanced technology.
Delivering customer satisfaction by adding values, seeking innovative solutions to help our customers achieve their goals and exceed expectations.
The thrust areas of MEEPL's are as follows:-
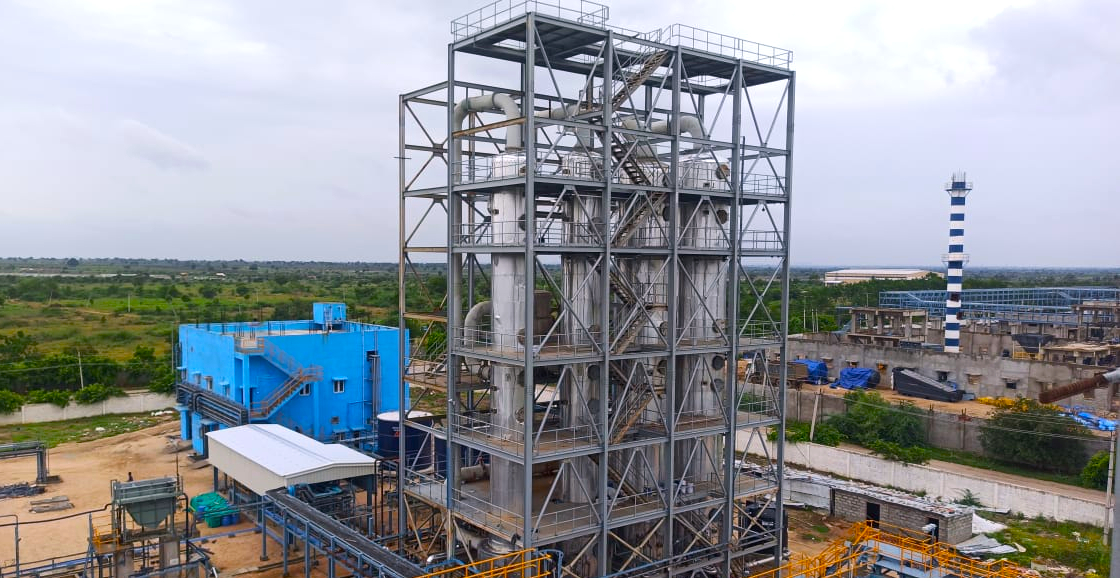
Dissolved Air Floatation System
- Dissolved air flotation (DAF) is a proven and effective physical/chemical technology for treating effluent stream.
- It is very efficient for the reduction of Chemical Oxygen Demand (COD) present in fat, grease, oil, biological sludge, coloured organic matter, and colloidal materials.
- DAF systems are used for the removal of oils & greases and suspended solids to meet a variety of treatment goals including:
- Product recovery and reuse
- Pre-treatment to reduce loading on downstream biological treatment systems
- Polishing of biological treatment effluent.
- Thickening of biosolids
Reverse Osmosis System.
- In RO system suspended and dissolved solids can removed by membrane filtration technology.
- RO system are used to purifying and recycling of waste water and make for reuse.
- Ro membrane filtration can treat High TDS of water .
- In this process, pressure is used to force effluent through a membrane that retains contaminants on one side and allows the clean water to pass to the other side.
Solvent Stripper
- It is removal process of solute gas from a liquid.
- Evaporation technology to remove the solvent present in the effluent.
- Due to pressure / temperature phase difference between the steam and contaminant allow the steam to strip the contaminants from the water.
- Plate and packing are the different types of solvent stripper .
- Stripper will remove 99% of VOC contents from the effluent.
Forced Circulation Evaporator
- High TDS effluent water is heated and circulated to increase the salt concentration.
- Multiple-effect evaporator plants, the downstream-arranged evaporation is heated by using the exhaust evaporators to reduce the consumption of steam.
Agitator Thin Film Dryer
- ATFD is the evaporation technology to prevent the scale formation in the Crystallizer and convert amorphous salt.
- To concentrate highly viscous products, polluted liquids, salt solutions.
- Operating pressure upto 1 mbar
- Residence time of few seconds, hence very useful for heat sensitive product
Gallery
HTDS
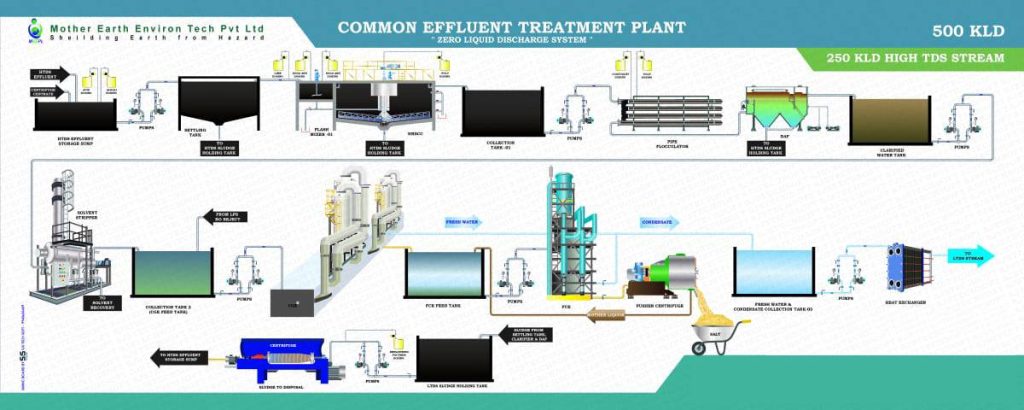
LTDS
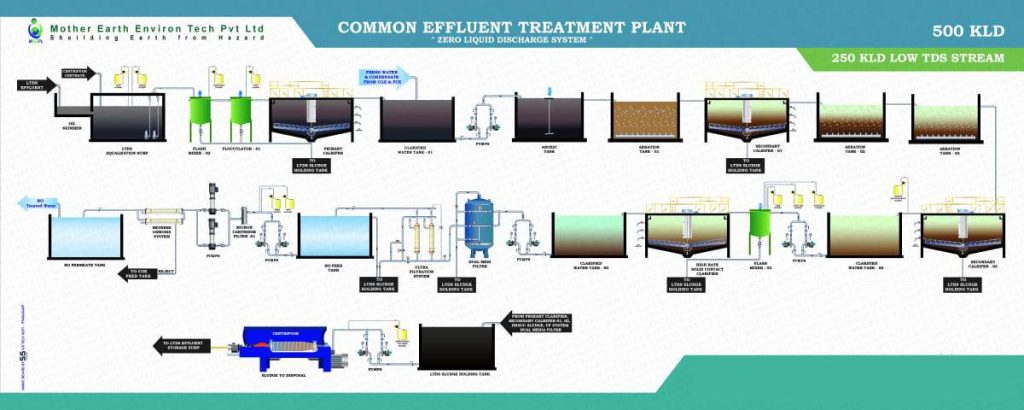